Aerojet Rocketdyne Increases Thrust Level of Bantam Engine by 500 Percent
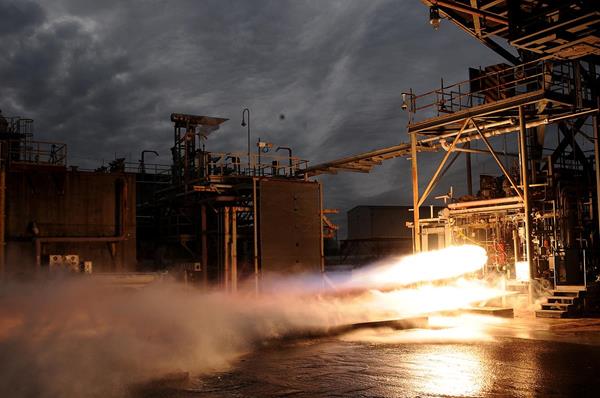
Aerojet Rocketdyne’s 30,000 lbf thrust class 3D-printed Bantam engine undergoes testing at the NASA Marshall Space Flight Center. Photo: Aerojet Rocketdyne.
Aerojet Rocketdyne recently completed a series of hot-fire tests on a 30,000 lbf thrust-class Bantam liquid-fueled rocket engine built with additive manufacturing. This is a 500 percent increase in the thrust level from the Baby Bantam engine the company 3D-printed and tested in June 2014.
According to the company, at the 30,000 lbf thrust level, this engine is ideal for the rapidly growing small launch vehicle and low-cost upper-stage markets. This latest milestone paves the way for Aerojet Rocketdyne to develop a family of low-cost rocket engines for booster, upper-stage and in-space propulsion solutions.
Under this activity funded by the Defense Advanced Research Projects Agency (DARPA), Aerojet Rocketdyne successfully completed a series of 17 tests of a Liquid Oxygen (LOX)/kerosene, regeneratively cooled, liquid rocket thrust chamber assembly that demonstrated the performance, durability and reusability of the design. These tests explored a range of engine operating parameters, conditions and run durations validating the design and applicability of the additive manufacturing technology and its benefits, the company stated.
The 30,000 lbf thrust-class engine, which would normally be comprised of more than 100 parts, is built from only three additively manufactured major components: the injector assembly, the combustion chamber, and a throat and nozzle section. These three major components are welded together to form a single thrust chamber assembly.
According to Aerojet Rocketdyne, it designed, fabricated and tested the Bantam engine in just seven months at a fraction of the cost of producing the engine using traditional fabrication methods.
“The results of this test program confirm that we are on the right path to take advantage of the advancements we’ve made in 3D printing technology as a key part of our strategy to deliver more affordable products to our customers while we maintain the reliability they’ve come to expect,” said Aerojet Rocketdyne Chief Executive Officer (CEO) and President Eileen Drake.